AddParts is the only industrial spare parts solution that reduces your inventory and your downtime at the same time using on-demand digital spares.
Why AddParts?
- Reduce downtime associated costs by up to 90%
- Replace components only when you need them, freeing up your cash flow
- Significantly reduce the costs of physical storage for critical parts
- Hours or days instead of weeks and months shipping internationally from OEM manufacturers.
- Reduction in downtime as on-demand deliveries within 5 to 7 days of an order from the UK
- Extend component lifespan
- Quicker deliveries as pre-scanned and in virtual stock on your customer portal
By having a virtual rather than physical stockholding you can significantly reduce your carbon footprint:
- Reduction of raw materials used in the production process and minimising material waste.
- Lowering CO2 footprint by minimising transportation, shipping and handling from a UK-based supplier
- Extending the useful life of your legacy equipment
- Reduction of maintenance and warehouse pollution
- Advanced design of lightweight equivalent components use less energy in moving assemblies making your production line more efficient
- AddParts are designed and manufactured using the ISO9001 quality system and the team pride themselves on the highest standards of quality
- The quality management system means that all materials are fully traceable
- All data and dimensions of components can be verified back to your original component and each stage of scan, stock and supply
- Certificates of conformity are supplied with all AddParts
- Custom sizing of components
- Custom change parts for your business not in prepacked sets from OEM
- Re-designed components to provide easy sizing changes to enable you to provide a greater range of packing sizes to customers
What is AddParts?
We Reduce the Cost of Downtime on Production, Manufacturing and Packing Lines
We have proven to have demonstrated these kinds of savings:
-
Up to 90% on component savings
-
Productivity increases of 30%
-
Downtime reduction of up to 80%
Use the calculator below to show what savings AddParts can bring to your business.
Manufacturing Business
per year
25
AddParts
in AddParts
Latest News and Case Studies
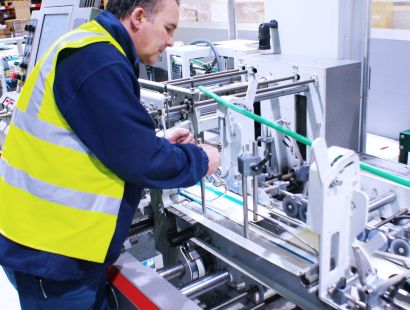
Chester Medical’s Print & Packaging Division – Contract Packing
How does AddParts work?
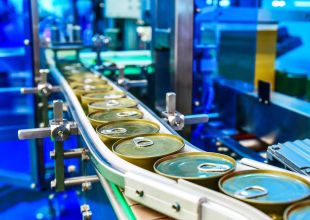
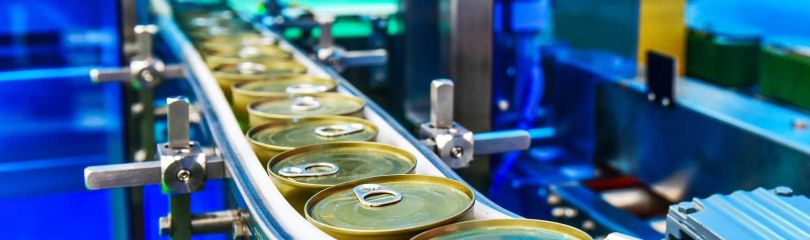
We recognise the costs and urgency of unexpected downtime from packing and production machine failure. Your priority is rapid, secure recovery. Our readily deployable digital spares service positions us as the premier first responders when downtime strikes on your automated production and packing line and our rapid callout service ensures a swift delivery, even if a critical component is not already held in virtual stock.
Our team are enthusiastic advocates for UK manufacturing and have over 20 years of experience in digital manufacturing, reverse engineering, design, additive manufacturing, materials regulatory affairs and production. To ensure that AddParts excels, we use three core technologies:
Scan
To minimise disruption and maximise efficiency, AddParts have invested in cutting-edge high-resolution, handheld laser scanning technology. The technology we deploy onto your site has been developed specifically for the range of components, scale of equipment and materials that are frequently found on production lines.
When on-site, we will quickly set up and calibrate our scanner and collect all of the information needed to replicate components – in some cases the entire machine bed as well as the parts. This can be a pre-arranged visit to coincide with planned shutdowns or in an emergency where a critical component has failed or been broken, we’ll be there within 24 hours.
By 3D scanning on your site, we can ensure that your disruption is minimised although we can also receive components at our dedicated facility in Sheffield if this is easier*.
AddParts scanning is charged on a day rate but whilst on site we will work quickly to scan as many parts as possible to maximise the value of this part of the service.
By using a high-resolution blue light laser scanner to scan components on your site, we ensure that disruption is minimised, and replacement parts are accurate and reliable.
* Not recommended for components which show signs of excessive wear.
Store
We understand that it takes more than one person to keep production going. Any storeroom needs to be maintained in an orderly way to give you the right information when you need it and that’s exactly what our AddParts portal gives our customers.
The 3D data we take during scanning and reverse engineering is held on a secure server allowing our customers to sign in, and view plant list and parts for each machine. Each component can be identified by part name/number or from the 3D data we hold as well as other critical information that we take during the scanning process. You will be able to view production costs, and accuracy information to verify that the part is accurate to the calibrated scan data as well as view previous order history and download a copy of certificates of conformity.
You can order the part from the portal, upload details for components not yet in stock as well as make bookings for site visits to coincide with planned shutdowns. Our portal is mobile friendly too meaning you can work with AddParts whilst you are on the shop floor.
By using virtual stock holding, our customers can see what parts they have, find out specific information about them, and order them when needed in a secure, well-organised place from a browser or a phone.
Supply
From day one, we have taken 3D printing seriously as a valuable, adaptable and reliable production technology able to cut it alongside moulding and CNC machining.
The team behind AddParts have over 20 years in using 3D print technology to produce accurate, durable, high-value products, devices and components in sectors as diverse as medical devices, pharmaceuticals, consumer products, safety equipment and food production. Together with a dedicated ISO9001:2015 quality management system and facility in the heart of UK manufacturing, we have built a unique capability which provides AddParts customers with the full benefits of industrial 3D print technology.
We have invested in the 3D computer-aided design technology needed to make the most of scan data in the most accurate way and provide validation data for this process accordingly, all made available on the AddParts portal.
We have a number of industrial 3D print systems taking advantage of both FDM and SLS technology, producing components in materials that offer capabilities including food and pharma contact, high durability, high strength and ultra-smooth surface finishes. We have selected these technologies specifically because of the benefits they bring to production equipment components and operate them in a way that will meet the requirements of any regulatory standard we are likely to find across the UK manufacturing sector.
Using industrial 3D printing, AddParts is able to maintain highly flexible, adaptable production capacity to meet the demands of our customers with high-quality, cost-effective and accurate components with short lead times.
* We will supply parts as quickly as possible. Our fastest turnaround lead time is 48 hours which assumes a single component from digital stock that has been ordered previously and that the part is dispatched by courier. Typical lead times are 5-7 working days for standard components and up to 15 working days for complex, multi-body components with post-production treatments and additional fittings. Please ask for more details on specific components.